Fiber optic sensor cables are the key enabler for real-time monitoring of temperature, strain, and acoustic signals across diverse and challenging environments. Depending on the application and the used technology standard fiber optic telecom cables are suitable, while other applications may require specialty cables. These specialty sensor cables are designed to deliver precise measurements, even in harsh conditions.
How the Technology Works
Optical fibers consist typically of three main components: the core, the cladding, and the coating. The core and cladding have different refractive indices, which affect how light travels through the fiber. By utilizing total internal reflection, light can travel long distances with minimal signal loss. The core's refractive index is higher than that of the cladding, allowing light to be contained within the core and propagate over kilometers with minimal attenuation.
To protect and strengthen the core and cladding, a primary coating is applied. The choice of coating depends on the temperature range and sensing technology. For standard temperatures, polyacrylate coatings are used, while polyimide or metal coatings are suitable for high-temperature or cryogenic environments.
Primary coating ambient temperature range
Primary Coating | Ambient Temperature Range |
Acrylate | -40 °C to +90 °C |
High temperature acrylate | -40 °C to +150 °C |
Silicone PFA | -40 °C to +200 °C |
Polyimide | -180 °C to 300 °C |
Metal | >300 °C up to +500 °C |
AP Sensing's sensor cables include the sensing fiber and come in various configurations, including metal-tubing, metal-free, tube-in-tube, and armored stainless steel. Metal-free cables are flexible and reduce the risk of induced voltages, while metal armored cables offer robust protection against harsh environments and rodent damage. We also provide different sheathings, such as flame-retardant non-corrosive (FRNC) and water-tight high-density polyethylene (HDPE), to meet specific environmental requirements.
Sensor cables are available with multimode (MM) and singlemode (SM) fibers or a combination of both. For MM fibers, typically a core of 50 µm or 62.5 µm diameter is chosen, which enables significantly more light to travel in the core than in SM fibers. Nowadays, a 50 µm core is preferred over 62.5 µm in most cases and has become the established standard for multimode fibers. Most MM fibers also have a graded index (GI) of their cross-section to reduce mode-dispersion. This means that the transition in index of refraction is gradual between the cladding and the core, as opposed to step-index fibers, where the refractive index sharply decreases from the core to the cladding (mostly used for singlemode fibers).
The main mode of light propagation is along the central fiber axis when an initial pulse of laser light is emitted into an optical fiber. If light enters the fiber at an angle to its centerline, this results in internal reflections causing the light to travel in the step-index (zigzag or spiral path) through the fiber.
Typically, MM fibers are used for DTS and for most high-bandwidth fiber optic communication links. MM fibers have substantially greater cross-sections that enable much more light (more energy), that are coupled into the core. Furthermore and compared to the core of a SM fiber, MM fiber minimizes the core alignment mismatch, so less light gets lost at splices and mechanical connectors. All this results in a better signal-to-noise ratio (SNR) and resolution performance for DTS systems.
However, SM fibers are advantageous for different systems. The SM fibers typically have a small core of 9 µm in diameter. By allowing light to propagate in only one mode, modal dispersion is minimized. Less light can be coupled into the fiber, so obtaining measurements from the Raman scattering signal is much more challenging. As the Rayleigh scattering signal is orders of magnitude more intense than the Raman scattering signal, SM fibers are most used for DAS or DTSS systems, as these systems utilizes the Rayleigh or Brillouin back scattering signal.
Fiber optic sensor cables are usable even at remote locations, as these cables are very small in size and need no electrical power to function. The sensor cables are also immune to electromagnetic interference (EMI) and do not conduct electricity, so they can be used in locations with high voltage electricity or the presence of flammable material such as jet fuel in airport hangars.
Benefits & Advantages
Precise Localization
Accurate detection and localization of temperature, strain, vibration, and acoustic events.
Broad Temperature Range
Operates across a wide temperature spectrum, from -180 °C to +300 °C.
EMI Immunity
Resistant to electromagnetic interference, ensuring reliable performance in challenging environments.
Maintenance-Free
Ideal for inaccessible areas, requiring no ongoing maintenance.
Explosive Hazard Safety
Suitable for use in explosive hazard areas due to its non-conductive nature.
Flexible and Passive
Small, flexible, and purely passive sensor elements enhance installation versatility and durability.
Comparison to Other Systems
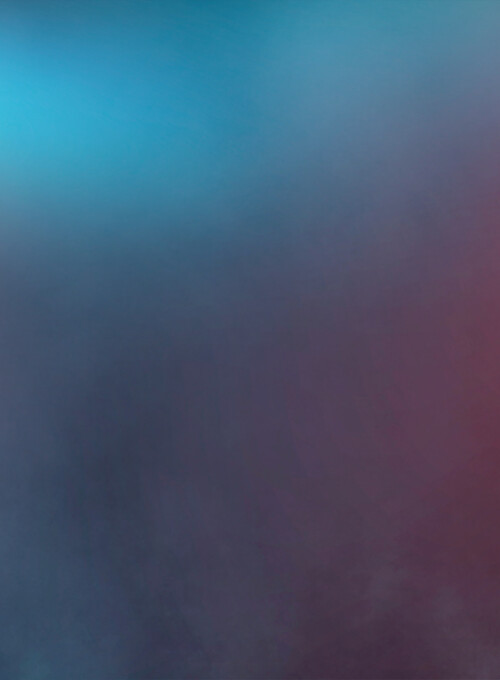
Applications of Sensor Cables
Power Grid Monitoring
Fiber optic sensor cables, using Distributed Temperature Sensing (DTS) and Distributed Acoustic Sensing (DAS) systems, enable real-time monitoring of power grids. They detect temperature hotspots, cable faults, and third-party intrusions, ensuring efficient load management, preventing outages, and enhancing the reliability of power transmission systems.
Fire Detection
LHD technology with sensor cables enables precise, real-time monitoring of temperature changes over large areas, making it ideal for tunnels, industrial facilities, and high-risk zones. Early detection of heat build-up allows for quick response to fire outbreaks, ensuring enhanced safety.
Pipeline Integrity Management
Fiber optic sensor cables enable continuous monitoring of pipelines, detecting leaks, temperature changes, and third party intrusion (TPI) activities. These systems ensure the safety and operational integrity of critical infrastructure in industries such as oil, gas, and water distribution.
Well & Reservoir Monitoring
Sensor cables are widely used in oil and gas wells for monitoring temperature and acoustic signals. These systems ensure the safe and efficient extraction of resources by detecting leaks, tracking well integrity, and optimizing production. Real-time data from the wellbore helps operators manage assets and respond swiftly to anomalies.
Geo-Monitoring
Distributed Temperature Sensing (DTS) and Distributed Acoustic Sensing (DAS) systems, using fiber optic sensor cables, are essential for monitoring environmental changes such as landslides, subsidence, and water table shifts. This helps mitigate risks to infrastructure and communities by providing early warnings and insights into potential hazards.
Railway Monitoring
Sensor cables in DTS and DAS systems monitor track integrity, detecting issues like rail buckling, broken rails, and unauthorized intrusions. These systems provide real-time data for proactive maintenance, reducing accidents and ensuring safer railway operations.
Perimeter Security
Sensor cables are used in perimeter security applications to detect unauthorized activities such as digging, drilling, or vehicular movement. These systems provide a highly accurate, real-time alert system for securing critical infrastructure like borders, data centers, and military bases.
Key Takeaways
Fiber optic cables represent a versatile and advanced sensor for a wide array of monitoring needs. Their ability to provide accurate, real-time data across extensive distances, combined with their immunity to electromagnetic interference and minimal maintenance requirements, makes them ideal for use in critical and challenging environments. From power grid monitoring to fire detection and energy exploration and many more, fiber optic sensors offer unmatched performance and reliability for modern monitoring applications.
Our team of application engineers will work with you on your project requirements to find a balance between costs, thermal conductivity respectively acoustic or strain coupling, and ruggedness.